The copper line of the LED advertising screen PCB is detached (also often referred to as copper throwing). The PCB factory says that it is a problem of laminates and requires its production plant to bear bad losses. According to the customer complaint handling experience, there are several common reasons for copper dumping in PCB factories:
First, PCB factory process factors:
1. Excessive etching of copper foils. Electrolytic copper foils used in the market are generally galvanized on one side (commonly known as ash foil) and copper on one side (commonly known as reddish foil). Commonly used copper flaring is generally more than 70um galvanized copper. Foil, reddish foil, and ash foil below 18um did not show mass rejection of copper.
When the customer circuit design is better than the etching line, if the specification of the copper foil is changed and the etching parameters are not changed, the residence time of the copper foil in the etching solution is too long. Because zinc is a kind of active metal, when the copper wire on the LED advertising screen PCB is immersed in the etching solution for a long time, it will lead to excessive corrosion of the line side, causing some fine lines of the backing zinc layer to be completely reacted with the base. The material detached, that is, the copper wire fell off.
In another case, there is no problem with the etching parameters of the PCB. However, after the etching, the water is washed and the drying is poor. As a result, the copper wire is also surrounded by etching liquid remaining on the surface of the PCB. If it is left untreated for a long time, the copper wire may also be over-etched. Throw copper. This situation generally appears to be concentrated on thin lines, or during periods of humid weather, similar defects appear on the entire PCB, and the copper lines are peeled off to see that the color of the contact surface with the substrate (the so-called rough surface) has changed. Unlike the normal color of the copper foil, the underlying copper color is seen, and the peel strength of the copper foil at the thick line is also normal.
2. Partial collision occurred in the LED advertising screen PCB flow. The copper wire was separated from the substrate by external mechanical force. This poor performance is poorly positioned or directional, and the shedding copper wire will have obvious distortions or scratches/impact marks in the same direction. Peel off the copper wire of the bad place and look at the matte side of the copper foil. You can see the normal color of the matte side of the copper foil. There will be no side corrosion failure, and the peeling strength of the copper foil is normal.
3, LED advertising screen PCB circuit design is not reasonable, with thick copper foil design too thin lines, it will also cause the line to etch over and throw copper.
Second, the laminate process causes:
Under normal circumstances, as long as the laminate is hot-pressed in the high temperature section for more than 30 minutes, the copper foil and the prepreg are basically completely bonded. Therefore, the press-fitting generally does not affect the bonding force between the copper foil and the substrate in the laminate. However, in the process of laminating and stacking laminates, if PP is contaminated or the copper matte surface is damaged, the bonding force between the laminated copper foil and the substrate may be insufficient, resulting in positioning (only for large panels and (Speaking) or sporadic copper wire falls off, but there is no abnormality in the peeling strength of the copper foil near the measured drop line.
Third, the reasons for the raw material of the laminate:
1, LED advertising screen above mentioned ordinary electrolytic copper foil are hair foil galvanized or copper plated products, if the peak value of wool foil production is abnormal, or galvanized / copper plating, plating defects, resulting in copper The peel strength of the foil itself is not enough. When the bad foil is pressed into the PCB to form a PCB, the copper wire will fall off under the impact of external force. Such copper splinters are stripped of copper wire to see the copper foil matte surface (ie, the contact surface with the substrate) will not be obvious after the lateral corrosion, but the entire surface of the copper foil peel strength will be poor.
Advantages of poor adaptability of LED advertisement screen copper foil and resin: Some special performance laminates currently used, such as HTg sheets, are not the same as the resin system, the curing agent used is generally PN resin, and the molecular structure of the resin is simple. The degree of cross-linking at the time of curing is low and it is necessary to use a special peak copper foil to match it. The use of copper foil when producing laminates does not match with the resin system, resulting in insufficient peel strength of the metal-clad sheet metal foils and poor copper wire drop-outs during the insertion.
Double
stations Vacuum Forming Machine
Double stations vacuum forming
machine applications
Double stations vacuum forming
machine is adapt for PVC, PP, PET, PEGT, OPP, POF, PS,
ABS etc, it can transform plastic sheets into various plastic blisters. These
blisters are widely used in hardware, stationery, commodity, electronic
products, health products, disposable cups etc.
It`s also suitable for the blister
packaging in toys, hardware, food, electronic products, medicine, commodity and
so on.
Double Stations Vacuum Forming Machine Features
1. Double mould
plates design, the heat furnace can heat to the two mold plate respectively.
The working efficiency is nearly twice as fast as that of the single mould
plate machine
2. 25pcs ceramic infrared heating boards which can be controlled
separately, suit for different size or different thickness material.
3. 25pcs Solid state voltage regulators, control heating boards simple and
visualized.
4. Large-scale cooling fan which can cool the products quickly.
5. Water-spray cooling system which suit for thick material.(optional)
6. Manual and Semi-auto style.
7. Button or pedal control available, improve the efficiency.
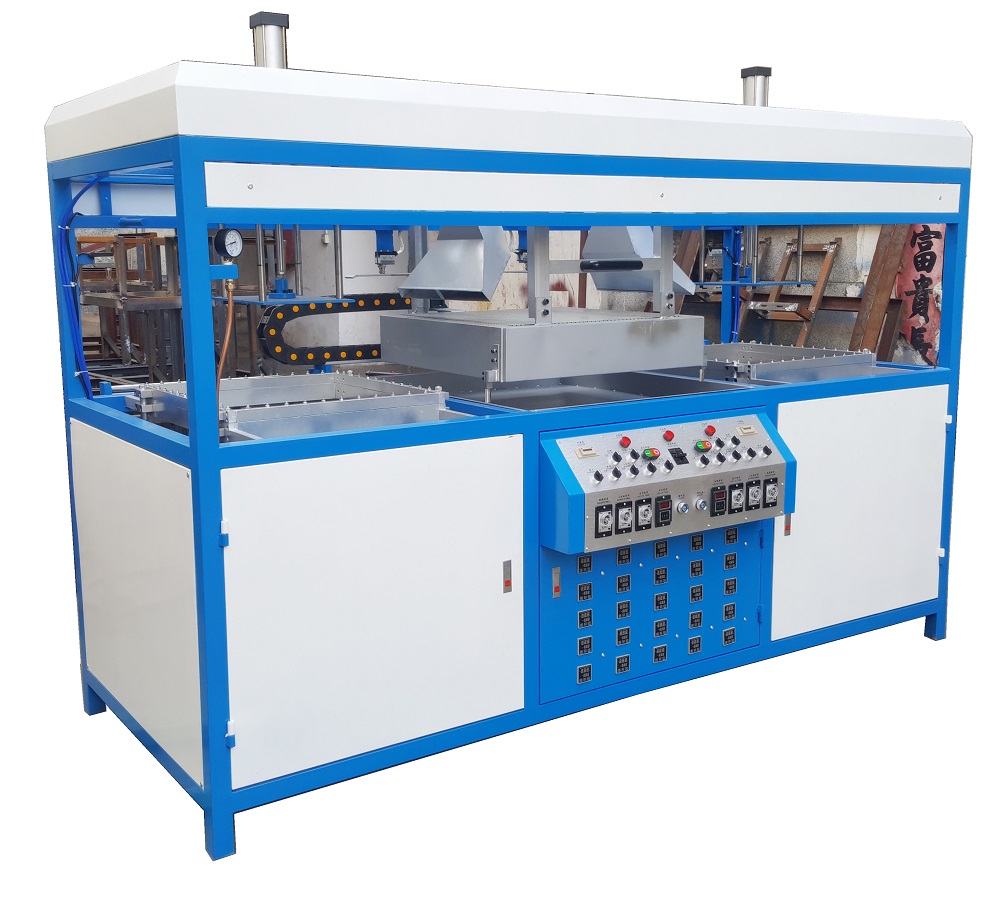
Double
stations vacuum forming machine Parameters
Model
|
HX-61A
|
Power supply
|
AC380V 50/60HZ
|
Power
|
13.0KW
|
Max. forming size
|
560*610mm
|
Max. forming height
|
200mm
|
Speed
|
300~500moulds/H
|
Thickness of material
|
0.2~1.5mm
|
Machine size
|
2700*1200 *2000mm
|
N. weight
|
1200KG
|